CNC Machining Services
One of the most effective methods for producing metal parts, or plastic components, with tolerances that are critical to function
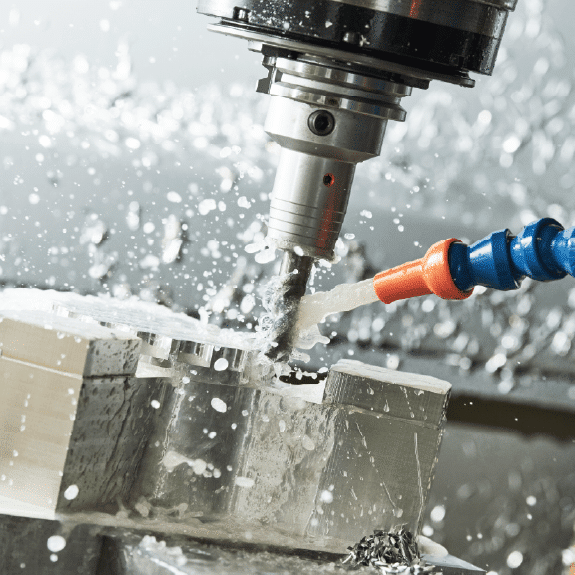
Precision CNC Machined Parts
Achieve consistent, high-quality parts for prototyping and manufacturing precision with CNC machining
From quick metal components to complex, mission-critical parts, A3D Manufacturing offers the right tool for the job at hand.
CNC machining allows for hitting tight tolerances and high repeatability with every order.
How CNC Machining Works
Rather than building parts layer by layer like additive technology, CNC machining starts with a solid stock piece and cuts away material – leaving behind a finished part.
Once finished parts are created, secondary options like smoothing, polishing, painting and more can be performed.
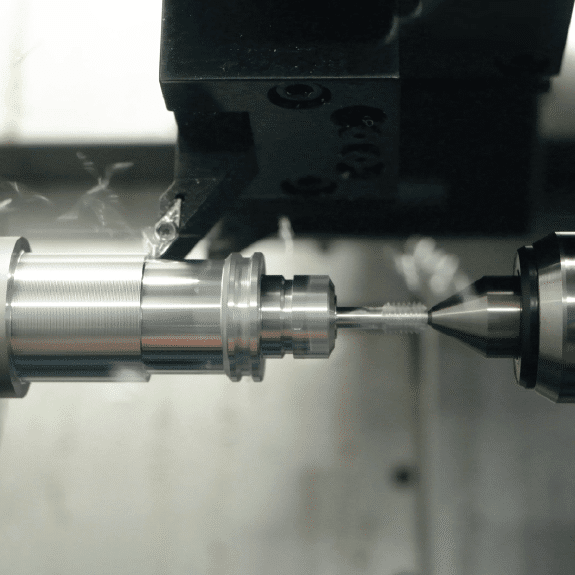
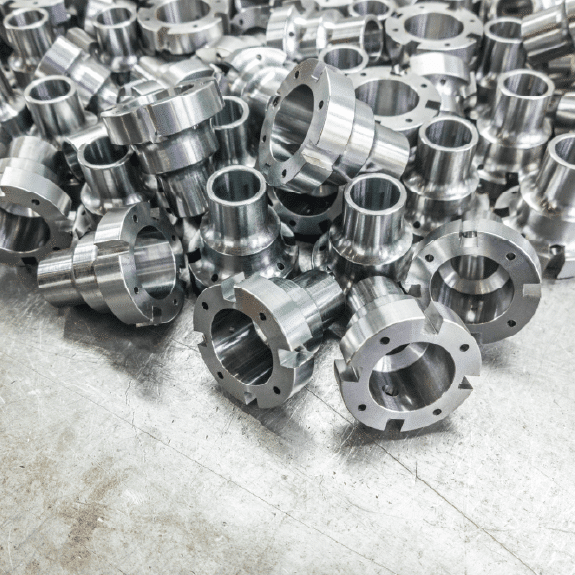
Common Applications
Explore popular uses for this traditional manufacturing method
- Medical
- Automotive
- Military
- Aerospace
- Consumer goods
Technical Specifications
|
CNC Machining
|
---|---|
Lead Times
|
Seven to 10 days.
|
Tolerance Accuracy Range
|
Default: +/- 0.005″ ○ Small features and holes: +/- 0.001-0.002″ ○ Features over ~10″ pick up ~0.001 in/in
|
Metal Materials
|
Aluminum 6061, Brass, Copper, Cold Rolled Steel, Mild Steel, Stainless Steel
|
Plastic Materials
|
ABS, Acrylic, Delrin, HDPE, Nylon, PEEK, Polycarbonate, Polypropylene, Ultem, Teflon
|
Frequently Asked Questions
Number of Operations
The location and accessibility of a part’s features will dictate how many set-ups or operations are required. Parts with multiple set-ups may suffer a small tolerance loss between features. Multiple operations can also affect a project’s cost and lead time.
Reach VS Width
Long, thin cutters deflect and break. When reaching into a deep pocket, keep radii large to accommodate a thicker, more robust cutter. Internal Stresses Residual internal stresses in the workpiece, coupled with elevated temperatures involved in the cutting operation, can cause parts to deflect. This effect is exacerbated when a large amount of material is being removed from a thin, flat workpiece.
Radii and Tool Access
Rotating cutting tools are essentially cylinders, meaning that internal vertical corners need a radius, if only a small one. If the cutting tool is unable to reach a feature, it cannot be CNC machined. Careful tool selection can reach some mild undercuts, but, as a general rule, all features should be line-of-sight. This effect is exacerbated when a large amount of material is being removed from a thin, flat workpiece.
Due to this process, some visible tool marks may be seen.
If additional finishing is required, please note in your drawings and in your request for quote.
Anodized, bead blast, chem film, passivation, and powder coat.