We live in the age of customization, where one can design and tailor anything from food to clothing. FitMyFoot proves that the same can be said for orthotics.
The FitMyFoot mission is to help people live more active and healthy lives. The company accomplishes this by providing custom, 3D-printed insoles and sandals. The FitMyFoot team started on this path when the company witnessed the tiresome process of getting custom-made orthotics.
“The whole process wasn’t exactly user-friendly,” Chris Jolley, CEO of FitMyFoot, said. “You had to go to a doctor, take specific measurements, wait a month or two and spend several hundred dollars on the products.”
FitMyFoot believed it could do better.
“We knew we were going to use 3D printing,” Colin Lawson, Director of Customization Technologies at FitMyFoot, said. “A lot of the early days were spent going to arthritis and foot doctors to see how they made their product to learn how 3D printing could disrupt the industry.”
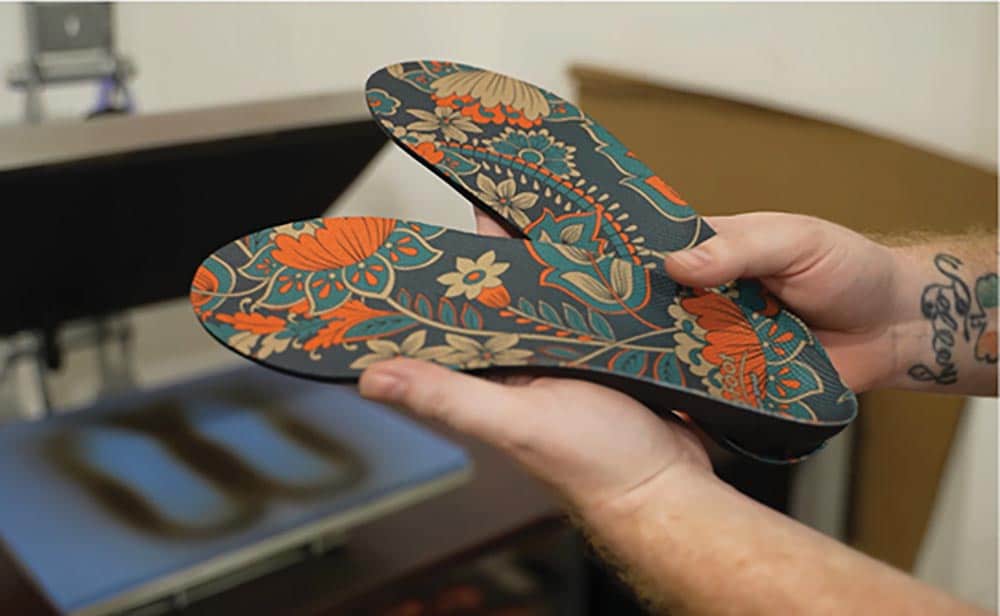
Lawson was integral in creating the algorithm that automatically creates a 3D print file from pictures of their customer’s feet. At first, they developed a corrective product for medical use, but they really caught their stride when they transitioned to comfort for everyone.
“It’s not just people who need to fix their ankles,” Lawson said. “Some people just want more comfort. So, we refined our product and started adding others.”
Additive manufacturing was the perfect solution for these products because it allowed for unique shapes at faster production speeds and lower costs.
After a few years, FitMyFoot partnered with A3D Manufacturing, leveraging our team’s years of 3D printing and manufacturing expertise. The footwear company switched to HP Jet Fusion 3D printers for even better results.
“The HP printers added a level of quality to the product, which is critically important for us,” Jolley said. “It gives us the ability to bring custom products like ours to the masses in a very cost-effective way.”
We explained to the FitMyFoot team how HP specializes in high-volume, high-quality production printing. Since every insole is unique to the person, the powder-based system is crucial for FitMyFoot.

The footwear company can fulfill hundreds of orders a week by nesting several parts in each build. Rivaling the production and cost of injection molded parts, the PA12 Nylon creates insoles that are built to last.
“It’s a really adaptable Nylon,” Lawson explained. “A few millimeters thick, and it is super stiff, but that would hurt your foot. If it is too thin, it will move too much with your foot. We can change that thickness throughout the insole and control it.”
Additive manufacturing makes FitMyFoot products more accessible, cutting down its cart-to-door time to ten days.
“The fact that you can get a custom part within two weeks of actually taking pictures on your phone — and having them uniquely made to the differences in your feet — is pretty amazing,” Jolley said.
FitMyFoot now has three products in its portfolio: insoles, slides and flip-flops. The company continues to expand thanks to the variety of applications provided by 3D printing, only limited by its own imagination.
“We are bringing such a unique product to market that truly helps people in their daily lives,” Jolley said. “It helps them feel better. It adds comfort to their everyday tasks.”
Contact us at A3D Manufacturing today and let us bring your custom ideas to life.